The choice of material is critical when prescribing a removable partial denture, as it directly impacts durability and comfort. Key factors, such as the available space in the mouth and the patient’s budget, also influence the most suitable option for a tailored treatment plan.
Based on our expertise, discover a selection of the best materials on the market and the most precise production techniques.
What are the different types of removable partial dentures?
A wide range of removable partial dentures is available to meet the needs of various treatment plans. These aesthetic, durable, and comfortable dentures are custom-designed for each patient, ensuring an optimal fit. Our removable denture options include chrome-cobalt frameworks, titanium frameworks, PEEK frameworks, Valplast prostheses, and Cu-Sil denture prostheses.
5 recommended materials for removable partial prostheses
1. Chrome cobalt
This alloy offers excellent elasticity while maintaining strength. 3D-printed at the laboratory, these prostheses provide precise thickness adjustments, enhancing durability. Digital processing, meaning using specialized software for 3D modelling, allows for meeting even the most specific technical requirements. Compared to traditional methods, computer-aided design and manufacturing (CAD/CAM) offer numerous advantages, including faster production times, greater customization, and unmatched precision. Our laboratory’s innovative laser printing technology eliminates metal porosity, allowing the prosthesis to better withstand mechanical forces without cracking. In contrast, with traditionally cast frameworks, obtaining the same level of durability is difficult.
Advantages:
- Lightweight and robust
- Digitally precise modelling
- Option to include nylon clasps
- Polished finish for optimal shine
Best suited for:
- Complex or uncommon geometries
2- Titanium
Titanium is lighter than chrome cobalt and an excellent choice for patients with allergies to chrome cobalt prostheses. It shares many advantages, including high elasticity and impressive durability. Like chrome cobalt, titanium benefits from a digital design and manufacturing process, resulting in a machined dental product with high resistance to mechanical stress. This innovative technique far surpasses the mechanical characteristics of cast prostheses.
Advantages:
- Digitally optimized design and manufacturing
- Option to include nylon clasps
- High-precision machined dental product
Best suited for:
- Patients allergic to chrome cobalt
3- PEEK
The primary advantage of PEEK is its high biocompatibility. Although its higher modulus of elasticity makes it less durable than chrome, cobalt, or titanium, the PEEK framework is the only viable option for patients allergic to metals.
Advantages:
- Can be combined with flexible nylon clasps
- Option to include nylon clasps
Best suited for:
- Patients with metal allergies
4- Injected nylon (Valplast)
The Valplast prostheses rest directly on the gum, eliminating the need for metal clasps. Nylon, known for its durability, is perfect for existing and added teeth. By combining nylon and metal, the benefits of both materials—flexibility, resistance, durability, and lightness—are leveraged. This hybrid production technique was developed in the laboratory and has been proving its worth for several years.
Advantages:
- Durable
- No metal clasps required
- Hybrid design with metallic framework
Best suited for:
- Patients allergic to chrome cobalt
5 - Injected silicone ring (Cu-Sil)
The Cu-Sil prosthesis, shaped like a ring, is a unique solution for patients with only one to four teeth remaining. The durable silicone ring surrounds the remaining teeth, ensuring stability in the mouth. Another interesting advantage is that this dental product is easy to modify after an extraction.
Advantages:
- No metal clasps required
- Easy to repair after an extraction
- Highly stable
Best suited for:
- Patients with only one to four teeth remaining
Efficient and precise fabrication process
Our collaborative design and manufacturing process ensures high-precision dental products tailored to each patient’s unique needs.
Key highlights of our manufacturing process include:
- Using physical or digital intraoral impressions to create a digital prosthesis model.
- Digital modelling for chrome cobalt, titanium, or PEEK dental products, enabling:
- Precise control over the thickness of the prosthesis for enhanced strength and durability.
- Elimination of errors linked to material expansion.
- Responsiveness to specific technical needs.
- Approval of the digital model through TrakDesign, an online platform developed by our team that simplifies the process from design to delivery, fostering seamless communication between the dentist and the lab.
- Polishing techniques vary based on the chosen material:
- Hand polishing preserves the product’s geometry while enhancing precision and shine.
- Scratch-free hand polishing ensures perfect finish without the use of pumice.
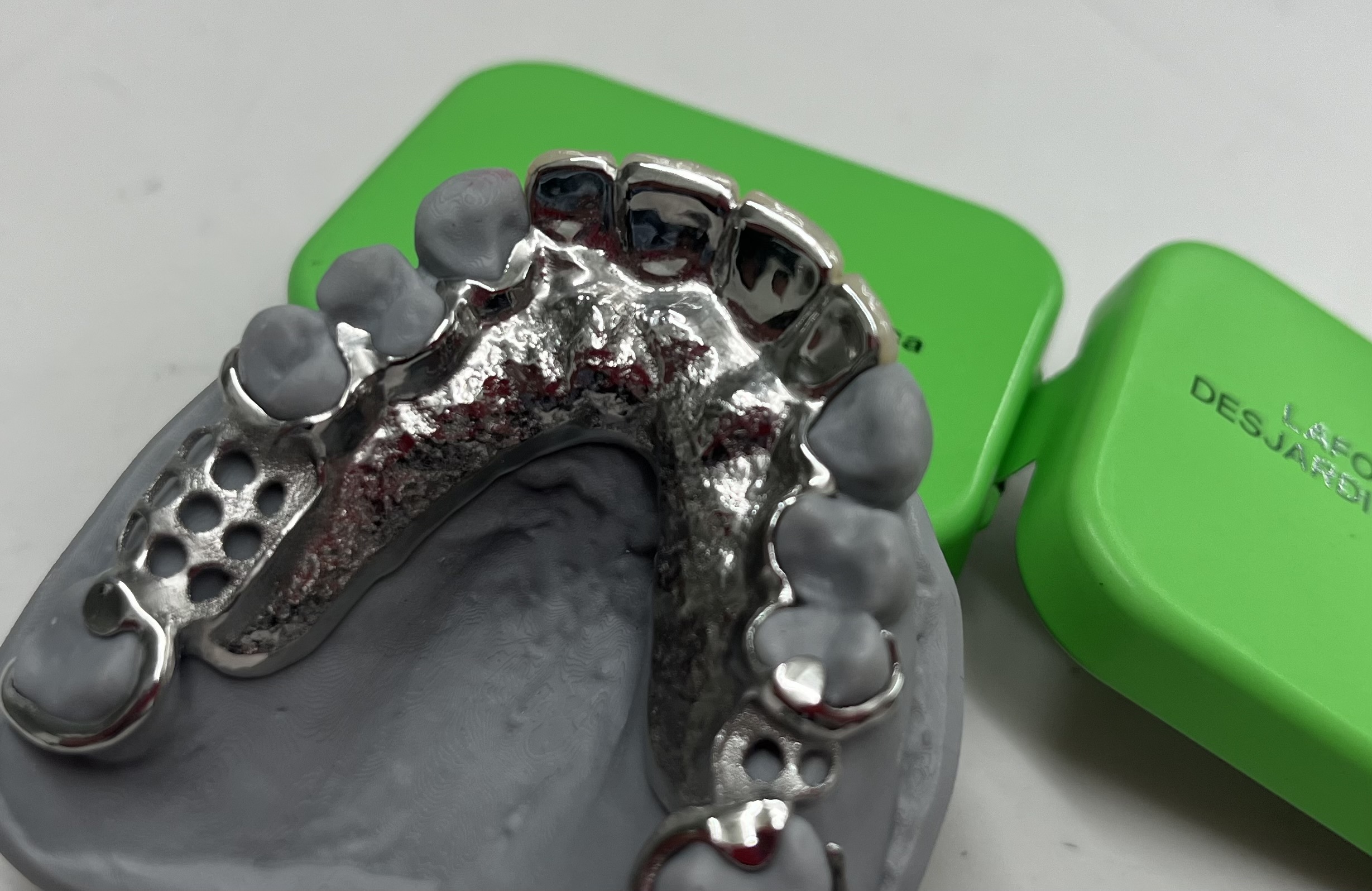
Restricted occlusal spaces
Metal lingual combination with buccal composite overlays and acrylic gum.
Unique dental cases: Limited occlusal or lateral space
A combination of a lingual metal framework and a buccal acrylic or composite solution may be used for limited spaces. The choice depends on the specific case.
A few essential steps must be completed before production can begin to ensure a result that meets treatment and patient expectations. Here’s our tried-and-tested process:
1- Evaluate whether creating a wax bite registration with a base plate is necessary to determine the patient’s precise occlusion.
2- A trial set-up, either digitally or physically, is performed to assess spacing and specific needs. Depending on the case or preference, this step can be completed by the denturist or the laboratory. Digital set-ups are created using TrakDesign, our proprietary platform. This tool allows seamless review and commentary on 3D models, facilitating efficient collaboration.

3- Choose covering materials according to the patient’s lifestyle and needs.
- Acrylic:
- A cost-effective option, though slightly less durable, as the incisal edges aren’t reinforced by metal. Moreover, a minimum of space is required for bonding, leaving a contact gap on the acrylic during propulsion movement. Our processes ensure that this is minimized to reduce its effect on durability.
- Teeth are selected based on moulds, colours, and brands, ensuring predictable aesthetics.
- Composite:
- A stronger solution, as the metal extends to cover the incisal edges entirely, and any contact points can be eliminated during the propulsive movement. However, this option is a little more costly, as the teeth are fabricated by hand, one by one.
- Enhanced aesthetic customization.
- Chemical bonding with metal makes it more durable than acrylic.
4- Assess whether a gum base is necessary. For patients with prominent natural gums, no pink gum material is included, ensuring a more aesthetically pleasing result.
Once the patient approves the prosthesis set-up, it will be used in the laboratory to craft the piece precisely, following the contours of the teeth.
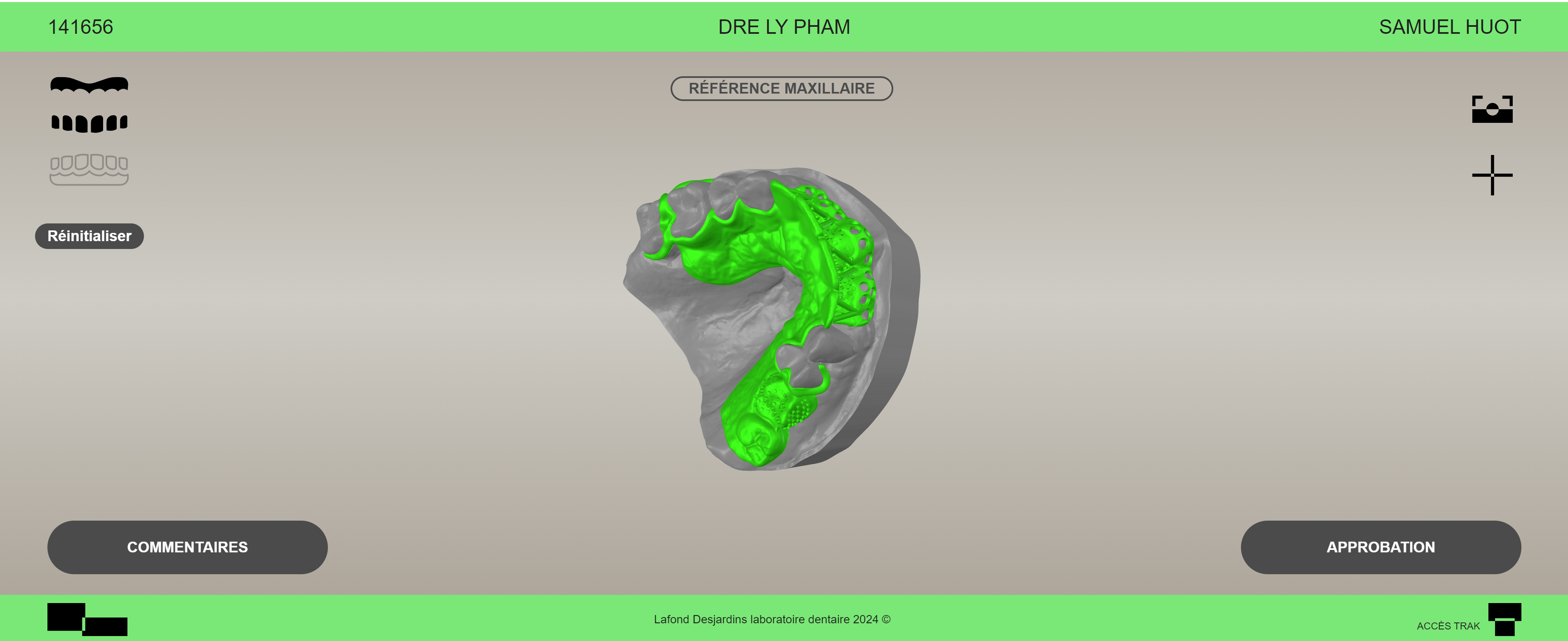
3D modelling of a partial prosthesis in TrakDesign, a platform developed by Laboratoire Lafond Desjardins.
In collaboration with our advisory team, select the materials best suited to your treatment plan needs. You can request a complimentary laboratory cost estimate to explore one or more options. This service allows you to compare solutions, inform your patient about associated costs, and consult with one of our experts to validate specific ideas.